- Concrete Repair Home
- Surface Repairs
- Structural Repairs
- Slab Repairs
- Concrete Crack Repair
- Common Concrete Repairs
- Stamped Concrete Repair
- Driveway Repair
- Pool Deck Repair
- Garage Floor Crack Repair
- Fix Spalling Concrete
- Make New Concrete Match Old
- How to Fix Pitted Concrete
- Concrete Repair Methods & Systems
- Concrete Crack Injection for Basements
- Why Concrete Cracks
- Sunken Concrete Foundations
- Repairing Bowed Basement Walls Using a Carbon-Fiber-Reinforced Grid
- Concrete Raising & Leveling Equipment
Leveling Uneven Patios, Pool decks, Walkways, Driveways & More.
Concrete Repair - the Best Products & Methods
Get advice on troubleshooting damage and coming up with the best concrete repair solution
Concrete surfaces are constantly under attack by
the elements resulting in the need for repairs.
Accuflex Coatings
Before you can repair anything you have to know what caused the problem in the first place and you have to understand how it is supposed to work. Only then can you make an intelligent decision on how to do the repair.
With any concrete repair, take that lesson to heart and you're off to a great start. First figure out what caused the damage, do the necessary preparation of removing any unsound concrete and contamination, then install a repair designed to solve the problem. The worst thing you can do is make a repair that doesn't last. Someone once told me that over 50% of concrete repairs fail again within two years. That is not a track record that inspires confidence.
The best method of concrete repair depends on the type of damage and whether your fixing a slab, driveway, pool deck, indoor floor, or other surface.
Need Help? Contact nearby professional concrete contractors to do your repair work.
CONCRETE REPAIR EVALUATION
The typical reason for evaluating concrete is that it is somehow damaged—we seldom evaluate the condition of perfect concrete. So what are we looking for when we evaluate damage? Start by deciding whether the damage is structural or superficial. A large diagonal crack across a concrete beam is serious and means it is time to call an engineer—don't take on the responsibility of structural work unless you know what you are doing. Document any structural problems you observe and contact the owner immediately. Just being there could impart some responsibility to you if there was a failure and you didn't take some action.



This doesn't look so bad on the surface, but the rust tells us that the reinforcing steel is deteriorating. The only solution is to remove the unsound concrete and replace with new. The Pascoe Group


If the concrete structure is not in danger of collapse, evaluate it in a series of steps, starting with a simple visual examination:
- Is the damage local or widespread?
- Is the damage superficial or does it go deeper into the concrete matrix?
- Is there damaged (corroded) reinforcing steel?
- For cracks, are they still moving?
- For surface delamination, can you define it as thin scaling or deeper spalling or is it an overlay delamination?
- What more extensive testing is needed?
- Do you have information about the initial construction (mixes, construction drawings, specifications)?
A good tool to have at this point in the investigation is a hammer and some spray paint. Pinging the concrete surface with the hammer will reveal delaminated areas that can be outlined with the paint. Delaminated areas send back a dull hollow sound instead of the hard ringing of sound concrete. Also be sure to have a tape measure to determine the extent of the repairs. Take lots of notes and photos—even video if that would more easily document the problems.
If you need more information you might have to resort to some destructive and nondestructive evaluation techniques. First, break away any damaged concrete to determine how deep the damage goes. Next, you can drill core samples for analysis in the lab or by a petrographer (someone who studies hardened concrete using microscopy). Non-destructive evaluation (NDE) techniques include radar, infrared thermography, and impact-echo, and can reveal a lot without having to open up the concrete.




WHAT CAUSES DAMAGE TO CONCRETE?
So we've done our evaluation and now we are ready to determine what caused the damage—this is often called troubleshooting. Start by thinking about the basic characteristics of concrete—strong in compression, weak in tension. Therefore, a crack implies that the concrete was in tension. Recognize that the crack is always perpendicular to the direction of the tension—always!
Think of a typical shrinkage crack running diagonally from a re-entrant corner in a concrete slab. The concrete was shrinking back in each direction from the corner and that diagonal crack is perpendicular to the direction of shrinkage. Look at a diagonal crack across the corner of a slab panel where it was run over by heavy traffic or the subbase was poorly compacted—the bending force created tension across the top of the slab. Take a saltine cracker and bend down the corner—it breaks in a diagonal line exactly the same as a concrete slab.
Here are a few typical concrete problems and their causes:
- Corrosion of reinforcing steel: Steel rebar is protected inside concrete because the concrete is very alkaline which prevents rust. But if there are chloride ions present, such as from deicing salts, the chloride destroys the "passivating layer" of alkalinity around the steel, allowing it to rust. Rust has greater volume than steel and the expansion presses against the concrete putting it in tension and causing it to crack and pop off. Chlorides get to the concrete through cracks or by simply penetrating through the concrete's pore structure.
- Freeze-thaw disintegration: Concrete is porous, so if water gets in and freezes it breaks off small flakes from the surface. Deicing salts make it worse. This is typically called scaling and it can occur during the first winter and get worse over time. When severe, it can lead to complete destruction of the concrete. Proper air entrainment completely prevents scaling.
- Alkali-aggregate reaction: AAR is a result of reactive aggregate in the concrete that forms a gel around the aggregate particle. When that gel gets wet it expands and can destroy the concrete. There are now some lithium products that can mitigate AAR.
- Drying shrinkage: Most concrete has more moisture in it when placed than is consumed by the hydration reaction. As that water evaporates, the concrete shrinks-about 0.15 inches over 20 feet, depending on how wet the concrete starts out. If you could hold a slab up in the air while it shrank, it probably wouldn't crack, but since it is on the ground it drags on the subgrade and the shrinkage is restrained and cracks form. Joints in concrete control the drying shrinkage cracks-at least joints let us decide where the crack will form. Learn more about concrete joints.
- Plastic shrinkage: When concrete is placed, if the surface is allowed to dry out before the concrete has gained strength, a pattern of cracks will form on the surface. This is also called crazing. These cracks are very shallow and narrow and are seldom a serviceability problem—although they can be objectionable to some owners, especially on decorative surfaces. The solution is proper curing, although synthetic fiber reinforcement can reduce this phenomenon.
- Blisters/delamination: Bubbled concrete surfaces may be blisters caused by prematurely finishing and sealing the concrete surface and sealing in air and bleed water. This can especially be a problem with air entrained concrete and heavy finishing equipment.
- Cracks from structural loads: Here's how reinforced concrete works: the steel reinforcement is completely useless until the concrete cracks. That crack my be very narrow, even invisible, but until the concrete cracks the steel doesn't start getting pulled to hold the concrete together. If there is no steel, inadequate steel, or the loads are too heavy (either during construction or in service), then the cracks can become wider. For a slab on ground that may not be significant, but for a wall or beam or column, cracks may signal structural problems. Learn more about structural concrete repairs.
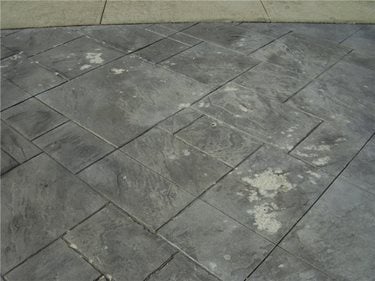
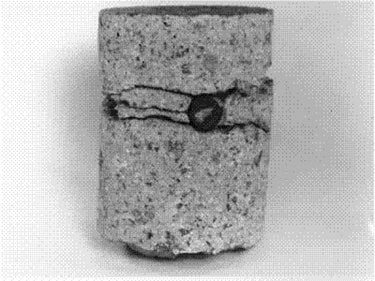
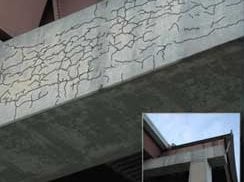
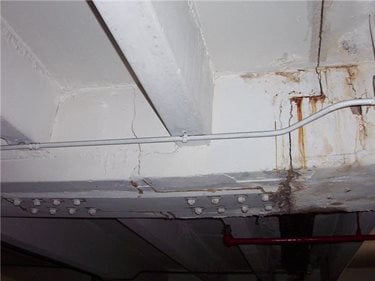
CONCRETE REPAIR MATERIALS
For some concrete repairs, the best repair material is simply high quality concrete. But manufacturers have developed some excellent repair materials that include various polymers leading to higher bond strength and durability. Most repair materials today are polymer-modified concrete, meaning that the basic material is a portland cement and aggregate mixture with a polymer (typically latex) added.
A couple of important factors in selecting a repair material are:
- Prior to deciding what repair material to use, make sure you know what the intent is: Are you trying to bond a crack together or just cover it up?
- Does the mortar need to stick to overhead or vertical surfaces? Or can it be very flowable to pour into forms or cracks?
- How quickly do you want the repair to achieve full strength?
- Do you want to use a one-part material or are you willing to use a two-component material that may be more difficult to work with but have superior properties?
- One of the most important characteristics of a good repair material is very low shrinkage. The concrete matrix has already gone through its shrinkage, so if the repair material shrinks, it will debond and the repair will fail.
- How important is bond strength? Usually very important--most repairs will be considered failures if the repair material doesn't bond to the concrete matrix. A big part of getting good bond is surface preparation.
- Consider the dimensional characteristics of the repair material: Drying shrinkage can debond a repair. If the repaired area will be under load, the elastic modulus should be similar. Thermal coefficients (the rate at which the material expands or contracts with temperature) should also usually be similar.
- Does the repair material need to be freeze-thaw resistant?
- Does the repair material need to allow water vapor transmission? Water vapor pressure from within the matrix of the concrete can create very high pressures-easily strong enough to debond many repair materials.
- How important is compressive strength or flexural strength? How about abrasion resistance?
Often, selecting the right material will mean compromising between several of these factors and, of course, cost. There are lots of good repair materials available—from W. R. MEADOWS, and many other companies. Figure out what characteristics you need in a repair material then talk with the manufacturer to get the best product for your application.
RESOURCES
If you are looking for more detail on a specific aspect of concrete repair, check out these outstanding resources:
- Concrete Repair and Maintenance Illustrated, Peter Emmons, published by R.S. Means. This book includes hundreds of drawings showing repair methods in detail. IT is currently on sale for almost half price.
- Concrete Repair Manual, published by the International Concrete Repair Institute, includes reference materials from ICRI, ACI, the U.S. Army Corps of Engineers, The Concrete Society (British), the BRE (also British), and much more. Over 2000 pages long—also available as a CD.
- The American Concrete Institute has several very good guides to concrete repair. ACI 224 is on crack repair, ACI 364 is on how to conduct a condition assessment, ACI 546 is an overall repair guide.