- Concrete Overlays Home
- Get the Look - Interior Overlay Pictures
- When to Use a Polymer Overlay
- Comparison Chart of Overlay Systems: Which is best for your project?
- Five Factors to Consider when Choosing a Resurfacing System
- Concrete Overlay Reviews
- Types of Overlays
- Epoxy Coatings
- Microtoppings & Skim Coats
- Self-Leveling Overlays
- Spray-Down Toppings
- Polishable Overlays
- Stamped Concrete Overlays
- Preparing Concrete for Resurfacing
- Concrete Resurfacing
- Reducing Bond Failures Caused by Moisture-Vapor Transmission
- Don't Let Water Vapor Delaminate Your Overlay: How to seal concrete before an overlay
- How-To Tips for Installing Concrete Overlays
- Answers to Common Questions About Concrete Overlays: Advice from expert Chris Sullivan
- How to Add Color to Concrete Overlays
- How to Protect and Maintain Resurfaced Concrete
- Overlay Tools: Seven essential tools for concrete resurfacing
- Related Information
- Concrete Overlay Videos, with Bob Harris
- Decorative Concrete Overlays: A primer of the various overlay types and the decorative possibilities with each
- Vertical Concrete Overlays: Lightweight cement-based overlays mimic stone, brick, and other wall textures
The Evolution of Decorative Overlay Products
An overview of the types of decorative overlays available on the market todayThis is an excerpt from the new e-book “Concrete Overlays Today,” part of a series of reports from ConcreteNetwork.com on trends and insights about decorative concrete applications.
Free E-book:
Concrete Stamping Today
Discover seven rising trends in the overlay industry from ConcreteNetwork.com’s new e-book. You’ll get insights and advice from veteran overlay installers that will help you find success in today’s market.
Download Concrete Overlays Today (PDF)
Decorative overlays can trace their roots back to commercial and industrial polymer-modified cement-based toppings introduced in the 1950s. Over the next 40 years, technological advances in dry ingredients and polymer technology led to stronger and more durable systems. Most of these were utilitarian, with little focus on the decorative market. By the mid to late 1980s, manufacturers started offering complete overlay systems targeting the growing decorative market segment. Those early-generation systems have evolved into the wide offering of decorative overlays available on the market today, including systems that work for both interior and exterior applications, on vertical and horizontal surfaces, and at thicknesses ranging from that of a credit card to an inch or more.
“Decorative overlay” is actually an umbrella term that covers a wide variety of products and systems intended to provide a decorative finish over an existing substrate. The general categories that fall under that umbrella are thin-section microtoppings, thick-section stampable overlays, self-leveling overlays and polishable toppings. Within each of these product categories are numerous individual products and systems designed for specific applications.
The one thing that all decorative overlays have in common is that they are polymer-modified, which increases their strength, adhesion and durability. When combined with cement and sand, these toppings can attain strengths exceeding 6000 psi. The additional strength provided by the polymer allows the cement-based material to be applied thinly without becoming brittle and weak. The final performance characteristics will vary greatly, depending on the type of polymer selected. The most popular types of polymers include acrylics, ethyl vinyl acetate (EVA), and styrene-butadiene rubber (SBR). Manufacturers will select the polymers they use in their overlay systems based on the target applications. Acrylics are usually found in systems for interior flooring, where a very hard, durable surface is needed and there will be little change in environmental conditions. EVA systems are more forgiving and are often found in overlays used for exterior applications or where flexibility is important. SBR polymers are used in systems that require water or chemical resistance. Of all the polymer resins being used, the most common is EVA because it produces overlays with a proven track record of performance at a comparatively low cost.
You’ll find most of these overlay materials and systems relatively easy to come by, with most full-line decorative concrete manufacturers offering at least one overlay product, and many offering multiple systems. The market has expanded to where multiple companies now specialize primarily in manufacturing and marketing decorative overlay systems and everything that goes with them. Distributors have also realized the demand and it is not uncommon for stores to stock multiple overlay systems, along with all the ancillary products and tools necessary for successful installation.
Related information:
Comparison Chart of Overlay Systems
Concrete Overlays
Return to Concrete Overlays Today






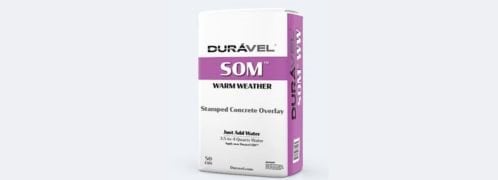
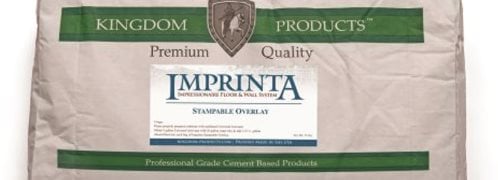