- Concrete slabs home
- Use a low water-cement ratio: How to calculate
- Subgrades and subbases for concrete slabs: Tips for ensuring good support
- Concrete Slab Finishing Tips
- DIY Slab Mistakes to Avoid
- How to Prevent Cracks
- Guidelines for preventing cracks in concrete slabs
- Be active in deciding where control joints will be placed
- Reinforcing Concrete Slabs
- Proper Curing of Concrete Slabs
- Properly curing concrete slabs: Why and how
- Related Information:
- Concrete fasteners
- Concrete forms
- The three types of concrete foundations
- Aggregates in ready-mix concrete
- Vapor barriers for concrete slabs
- Post-tensioned concrete slabs
- Concrete slabjacking
- Concrete testing
When to Use Fiber-Reinforced Concrete
Learn more about using synthetic fibers to reinforce concrete driveways, sidewalks, and more.You’re having a new concrete driveway installed, and your contractor recommends that you reinforce the concrete with synthetic fibers to make it more durable and crack resistant. But is adding fibers to your concrete always a good idea? And can synthetic fibers be used instead of or in addition to steel concrete reinforcement, such as rebar or welded wire mesh?
Whether you are a homeowner planning to install a new concrete driveway or a contractor looking for the best reinforcement option, it’s important to know the pros and cons of using synthetic fibers and how they compare with steel reinforcement. To help you make an informed decision, here are answers to some of the most commonly asked questions about fiber-reinforced concrete.
What are synthetic fibers for concrete?
Synthetic fiber reinforcement (also known as fiber mesh reinforcement) is a type of secondary reinforcement consisting of small polypropylene or polyethylene fibers that are mixed right into the concrete as a way to reduce cracking. You can also find fibers made of alkali-resistant cellulose, which are used in a similar manner as synthetic fibers but are made from processed wood pulp products.
Generally, there are two different types of synthetic fibers: microfibers and macrofibers. Microfibers are primarily used in concrete to improve impact and abrasion resistance and minimize plastic shrinkage cracks, which are irregular cracks that can occur in concrete within the first 24 hours after placement. After that time, however, their ability to control cracks is limited.
Macrofibers, as the name implies, are larger fibers (typically greater than 1-1/2 inches in length) with a ridged profile that allows them to bond with the concrete more effectively. An advantage of macrofibers is that they have the ability to minimize both early and later-age cracking of concrete. Because of this, macrofibers are often used to replace welded wire mesh and conventional reinforcing bars in a wide variety of applications, including driveways, sidewalks, floors, and other slabs on grade.
Learn more about why concrete cracks.
How is fiber-reinforced concrete made?
Fiber-reinforced concrete is basically standard concrete with synthetic fibers mixed evenly throughout before it’s placed. Because the fibers are uniformly distributed within the concrete, they provide reinforcement throughout the entire concrete slab, from top to bottom.
To ensure the proper dosage rate (which can vary depending on reinforcement requirements), synthetic fibers are usually supplied in degradable mixer-ready bags containing the recommended dosage for a cubic yard of concrete. The bags can be added to the concrete at the ready mix plant or thrown into the truck mixer at the jobsite. However, the concrete must be mixed at high speed for at least 3 to 5 minutes prior to pouring to ensure that the fibers are evenly and uniformly dispersed.
What are the advantages of fiber-reinforced concrete?
Using synthetic fibers to reinforce concrete offers a variety of benefits:
- They provide early crack prevention by controlling plastic shrinkage cracking as the water evaporates from the concrete. When a crack forms, the surrounding fibers will bridge the crack.
- They improve overall tensile strength and impact resistance by providing three-dimensional reinforcement.
- Unlike rebar, synthetic fibers can move with the concrete as it expands and contracts due to thermal changes, which can improve freeze-thaw resistance.
- Fiber reinforcement can be used to reinforce thin sections of concrete where steel reinforcement is not feasible, such as overlays and concrete repair work.
- Fiber mesh concrete is easier to place and eliminates the time and labor involved to install steel rebar or wire mesh.
- Unlike steel rebar, synthetic fibers are not susceptible to corrosion, which eliminates worries about rust spots appearing on the concrete surface.



What are the disadvantages of using fibers in concrete?
While there are many advantages to using synthetic fibers, they also have several drawbacks:
- The fibers must be mixed into the concrete thoroughly to provide uniform reinforcement. If mixing is done improperly, the fibers can ball up, resulting in inconsistent dispersion.
- Compared to standard concrete, fiber-reinforced concrete is more expensive, increasing the cubic yard cost by about 10%, depending on the dosage. However, if the fibers are used to reduce or eliminate the need for steel reinforcement, they can be more cost-effective overall.
- Adding fibers can result in slump loss and increase the stiffness and cohesiveness of the concrete mix, which may make the concrete more difficult to place. To maintain the desired slump and improve workability, it may be necessary to add a water-reducing admixture to the mix.
- To avoid exposed fibers on the surface of the slab, vibration of the concrete is usually necessary to bring more paste to the surface and bury the fibers out of sight.
Can you substitute synthetic fibers for rebar or wire mesh?
Depending on the project, synthetic fibers can be a viable alternative to steel rebar or wire mesh or it can be added to steel-reinforced concrete to lower the amount of steel required. In fact, some contractors have completely switched from using rebar or wire mesh to using synthetic macrofibers to reinforce concrete driveways and other load-bearing slabs. Before eliminating all steel reinforcement in a slab-on-grade, however, it’s best to consult with a structural engineer. The final decision will often depend on factors such as slab thickness, subgrade conditions, and the amount of traffic the concrete will receive.
Note that an advantage of using fibers in lieu of welded wire mesh is that you eliminate the concerns about the reinforcement not being installed properly. If the wire mesh ends up on or near the ground from being stepped on as the concrete is placed, it will become ineffective at controlling cracking.
Does fiber mesh concrete crack?
Synthetic fibers can significantly enhance concrete performance, but they won’t guarantee crack-free concrete. However, if fiber mesh concrete does crack, the fibers will intersect the cracks to inhibit their growth.
Is fiber-reinforced concrete good for a driveway?
Residential concrete driveways. sidewalks, and garage floors are all common structures where adding fibers to the mix can be beneficial to help control plastic shrinkage cracking and improve overall durability. However, for driveways that may be exposed to heavy traffic or movement caused by frost heaving of the subgrade, steel reinforcement may be needed to provide the necessary support.
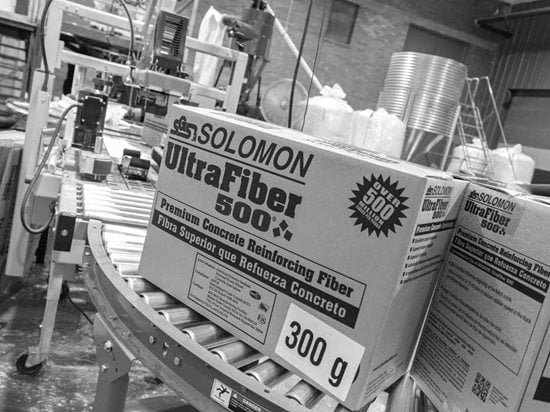
UltraFiber 500® can be mixed into small batches of concrete or added to ready mix trucks.
Do fibers interfere with decorative concrete finishes?
No. Synthetic fibers are compatible with most concrete surface treatments and finishes, including stamping, exposed aggregate, brooming, and acid-based stains. If any fibers protrude above the slab surface, they usually wear off quickly under light traffic. Because the fibers are neutral in color and won’t corrode, they also won’t stain or discolor concrete.
If you've struggled with fibers leaving the concrete surface fuzzy or hairy, try UltraFiber 500® from Solomon Colors. This fiber actually absorbs the concrete color and doesn't stick out of the surface. You get the added strength without compromising the look.