- Staining Concrete
- Stamped Concrete
- Concrete Overlays
- Concrete Resurfacing
- Concrete Polishing
- Concrete Dyes
- Colored Concrete
- Indoor Concrete
- Concrete Floors
- Concrete Countertops
- Garage Floor Coatings
- Furniture, Sinks, Fire Bowls
- Basement Floors
- Outdoor Concrete
- Concrete Patios
- Concrete Driveways
- Concrete Pool Decks
- Outdoor Kitchens & Counters
- Outdoor Fireplace
- Concrete Walkways
- Concrete Pavers
- Concrete Walls
- Repair & Maintenance
- Foundation Repair
- Concrete Crack Repair
- Concrete Sealers
- Building with Concrete
- Concrete Homes
- Concrete Basements
- Decorative Concrete
- Fire Resistant
A Guide to Concrete Efflorescence
What is efflorescence? What causes it? How do you prevent and remove it?Efflorescence is a fact of life with most concrete. We are hearing more about efflorescence related issues because of the popularity of stained floors. As the trend to have exposed concrete floors grows, the industry is struggling with the problem of unsightly efflorescence, especially when it is trapped under a film forming sealer. This is not to say that exterior decorative concrete is immune from efflorescence issues, but problems with interior floors pose a greater challenge and are the focus of this discussion.
This article is meant to be a common sense overview of the major efflorescence issues. We will suggest realistic preventative measures to control the conditions that encourage efflorescence and we will offer remedial suggestions. We will offer useful explanations of this complex phenomenon in practical terms without a lengthy detailed chemical analysis.
Find concrete cleaning products
Need a pro to fix your efflorescence problem? Contact a concrete contractor near you.
Decorative concrete contractors usually get the first phone call when efflorescence shows up on a stained floor. Many things may have contributed to a particular efflorescence plagued project, the least of which may be the work performed by the stain contractor who in most cases is unaware of the preexisting conditions that caused the efflorescence. Stain contractors, concrete finishers, builders, general contractors, the design community and owners are all affected by issues related to efflorescence. We hope this discussion clarifies some of the issues so that efflorescence is better understood and the appropriate measures are taken to prevent its occurrence. The costs associated with efflorescence prevention are minimal when compared to the cost and inconvenience of the remedies, especially when the space is occupied. Efflorescence in itself is not a health problem although it might indicate moisture levels sufficient to support mold. Efflorescence is not a structural issue. It is an aesthetic issue, an issue we would all like to avoid.
WHAT IS EFFLORESCENCE?
Efflorescence is the white powdery substance on the surfaces of unsealed concrete and the white blush seen with sealed floors. Efflorescence is caused by vapor migrating through the slab bringing soluble salts to the surface of the concrete. Efflorescence is normally worn off or washed away on unsealed concrete surfaces. In stubborn cases, a mild acid rinse or even a light sandblasting may be necessary. Efflorescence that becomes trapped under sealer is unsightly and is even more conspicuous on darker floors.
In worst case scenarios where the vapor cannot pass through the top coat, a urethane and/or an epoxy for instance, hydrostatic pressure can build to create water blisters indicating delamination of the top coat from the concrete. Blistering is rarely seen with acrylics. Acrylic sealers allow the vapor to pass through, but the salt deposits remain behind creating the unsightly blush that prompts owners to call the stain contractor.

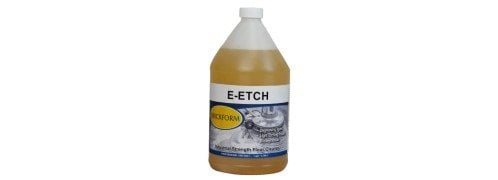

WHAT CAUSES EFFLORESCENCE?
Efflorescence requires the movement of moisture. Without moisture movement there would be no efflorescence on the surface to create the problem. Unfortunately, too many finishers (non-ACI Certified Finishers) routinely introduce large amounts of unnecessary "water of convenience" to the mix in order to facilitate concrete placement.
Primary efflorescence is caused by the water in the concrete evaporating from the slab leaving behind the soluble salts on the concrete surface. The fact that these salts are actually more soluble in colder temperatures coupled with increased bleed water in cold weather increases the likelihood of efflorescence showing up after winter concrete placement. Contributing further to efflorescence with cold weather pours is the use of calcium chloride to accelerate the set time. High slump concrete and the addition of calcium chloride are major contributors to efflorescence.
Secondary efflorescence is often described as water coming from underneath the slab or water that is introduced from the surface. Likely sources of secondary efflorescence would be a saturated base material, an improperly drained site or excessive amounts of water used by the decorative flooring contractor during his cleaning process - rinsing off the acid stain residue, for example. When extra mix water and extra soluble salts from calcium chloride are added to concrete placed in cool weather followed by more water from the decorative processes, some degree of efflorescing is bound to occur.
HOW TO REMOVE EFFLORESCENCE
What are the options when efflorescence rears its ugly head? A fast fix might be to use toluene, xylene or another coat of solvent base acrylic which reemulsifies the original sealer and clears the blush. If vapor continues to come up through the slab though, the condition will most likely reappear. Be aware that if the space is occupied there can be health issues because of solvents like toluene and xylene.
The most prudent course of action includes stripping the sealer in order to conduct a test to determine the rate of vapor transfer and then develop a remedial strategy. It is important to get it right the second time so take time to diagnosis the causes as best you can with the information available. One of the more expensive hand held digital instruments may prove to be a valuable tool because they are able to get accurate moisture reading below the surface of the slab. Once the moisture levels are established a sealer can chosen based upon the manufacturer's recommendations.
Remember that some manufacturers have the vapor inhibiting, non-film forming sealers that we mentioned earlier. These may reduce the vapor transmission rate to a level appropriate for a heavier bodied more abrasion resistant top coat for use in high foot traffic situations.
Where slabs have continued to have efflorescence problems even after the application of a lithium or silicate densifier contractors have used a finish or polish, which are industrial grade "mop and glow" - low build, low solids micronized acrylic water based products as the final treatment. These finishes and polishes can also be used over film forming sealers to add abrasion resistance.
In most efflorescence cases, the decorative flooring contractor inherited the problems that contributed to creating the efflorescence. Diagnosing the causes of efflorescence after the floor has been sealed can be difficult. It is important to determine how much moisture exists in the slab, the source of the moisture and also whether conditions, like seasonal ground water might contribute more moisture in the future. Consider vapor testing and resist the quick fix. Finally, contractors may elect to avoid warranty language where sealers are concerned or they may choose to specifically define typical vapor transmission problems. The decorative adage of "test, test, and test" holds especially true for interior stained floors. It means doing a VTR test whenever you suspect there may be the potential for efflorescence problems. Happy staining and remember – you don't have to take every job that comes your way.
HOW TO PREVENT EFFLORESCENCE
Efflorescence reducing measures are: site surface drainage; a well graded concrete mix with a water reducer to minimize paste; concrete not exceeding a 4" slump; that the concrete be well consolidated (one man vibratory screeds do a great job); placed directly on a vapor retarder and cured in some fashion. All these factors contribute to a concrete that has a minimum amount of bleed water with a lesser pore and capillary network that will resist rather than facilitate absorption and movement of moisture...in other words, a dense and relatively impermeable concrete slab.
Now for more specifics...an option to the vapor retarder is a waterproofing admixture to help prevent efflorescence. This is added to the concrete at the plant, but it has a downside. It can pose real problems for the stain contractor since a common ingredient, stearic acid, is hydrophobic in the same way that powdered release agents for stamped concrete are so the waterproofed concrete does not readily accept either acid stains or water base stains. Suggestions in this case would be to open the surface with a sanding screen or a gelled acid to create some degree of profile enabling a better mechanical bond for the water borne stain.
Not an Uncommon Set of Circumstances:
Scenario of potential efflorescence consequences of a fast track project:
Imagine the consequences of a fast track project...restaurants have to be the worst...with an acid stained floor on a slab as we just described, a few months old poured late in the year. The grand opening is early spring. The decorative contractor, being the sincere person he or she is, has proposed an upgrade from the acrylic sealer in the specifications to an epoxy or urethane because of the heavy foot traffic. The suggestion was approved, epoxy sealer it is. Our contractor goes into the project without a clue about the sub grade conditions, vapor retarder, mix design, admixtures, etc. There is one more complication all too familiar to staining contractors...the schedule. The superintendent greets our contractor friend on Monday with the news that the floor needs to be serviceable Friday morning so that the kitchen stoves and ovens can be dragged in. Our contractor feels a bit overwhelmed, but plans the work: clean up the drywall mud today; stain tonight; clean the residue Tuesday, apply epoxy Wednesday, Thursday is cure day, Friday is open for light traffic. This seems workable, life is good. No matter that the heat is not yet on in the building and the floor is not fully cured out. Our contractor friend, by the way, does not have floor scrubbers. Mops and buckets make up the clean up and water removal equipment. This is not an uncommon set of circumstances. What do you suppose the chances are that the stained and sealed floor will escape with no efflorescence?
Helpful mix design factors include ordering a well graded a mix from the ready mix producer. The advantage gained from a well graded mix design is the reduction of the weakest part of concrete, the cement paste (cement and water), making for a denser concrete than with a standard mix. Another important mix design consideration is the replacement of 15% to 20% of the Portland cement with fly ash which contributes significantly to lessening efflorescence. Fly ash brings three important benefits to reducing efflorescence. Fly ash reduces the amount of Portland cement and free lime as well as chemically binding up a portion of the free lime and salts that cause efflorescence. In addition, fly ash requires less water again resulting in a denser paste which aids in keeping moisture from traveling up from the bottom and from the top down. Water reducers of course, are also helpful at minimizing the amount of water and a reduction of cement (paste).
The closer a mix design gets to the desired water cement ratio of .45 pounds of water to pounds of cement, the fewer efflorescence issues arise, especially with a mix including fly ash. And forget the old notion that you can't use integral color with fly ash, you can. Keeping multiple pours consistent with the mix design, sub grade conditions and finishing practices will produce consistent results. Heads up on this one... cold concrete and cold ambient temperatures encourage efflorescence because the salts are actually more soluble in colder temperatures plus concrete tends to bleed more in cooler weather further encouraging the upward transportation of moisture and its passenger, soluble salts. Follow ACI 306 Cold-Weather Concreting procedures whenever possible including raising the placement temperature of the concrete to 60 degrees and then cover overnight to retain the heat. This will encourage a more dense pore and capillary structure and help close down the moisture transportation routes.
Curing becomes important as we recognize that moisture moves much more slowly through denser concrete from either direction. When concrete is kept moist for a longer period, especially the first few days, more capillaries and pores fill partially or completely to form a denser and more impermeable matrix that discourages the migration of moisture and soluble salts. Conversely concrete that is placed at a high slump and not cured acts as a sponge, full of miniature raceways allowing easy movement of moisture from the bottom up and top down. Cure and seal membrane type cures poses a problem in that the membrane has to be removed to accept acid stains, so they are not often used. One manufacturer has a thermal degrading wax that breaks down with hot water. Water borne stains are becoming popular and manufacturers are working to formulate compatible curing membranes that will accept subsequent staining. Wet curing is difficult because it must be continuous and may create discoloration if a plastic sheet has wrinkles.

Some contractors are following the application of acid stains with silicate type non-film forming sealers generically described as chemical hardeners, densifiers and soluble chloride reducers within a few days of concrete placement.

A Calcium Chloride Test is a good surface moisture test for determining the current vapor transmission rate of concrete. Photo Courtesy of Vaporprecision, Inc.
TESTING FOR VAPOR TRANSMISSION
Even if some answers are provided it behooves the contractor to do some independent fact finding to determine the current vapor transmission rate (VTR). Probably the oldest test method is the Plastic Sheet Test (ASTM-D-4263) which is taping down a clear 18" X 18" sheet of poly and checking 16 hours later for condensation or for a darkened concrete surface. Both are indications of vapor transmission. Another surface moisture test is The Calcium Chloride Test which quantifies the rate of vapor transmission. This is a covered dish that is weighed before and after a twenty four hour period. Both are cost effective measures in determining whether vapor is active.
A note of caution when using these testing methods...the plastic sheet and chloride tests will track moisture movement near the top only. When the atmospheric conditions are similar to the slab conditions the tests might not indicate significant vapor transmission because movement happens when the ambient conditions differ from the slab conditions. Moisture migrates and moves toward cool temperatures. Vapor emissions migrate and move toward heat. Imagine the consequences of the following unpleasant, but very real scenario... the project is completed, the contractor has been paid, the delighted owner takes possession and turns on the HVAC causing vapor in the slab to move towards the warmth or the lower humidity of the conditioned space bringing the whitish minerals with it. If the sealer is acrylic the vapor will pass through leaving the efflorescence. If urethanes or epoxies are on the floor, hydrostatic pressure may build and possibly cause delamination. Efflorescence can occur months or even years after the contractor has left the job due to circumstances similar to those just described or from seasonal ground water seeping under the slab. Testing the surface may not be enough to guarantee an efflorescence free project for years to come. It is important to determine the source and the rate of vapor transmission before prescribing a remedy.
Determine ahead of time if efflorescence is a likely problem waiting to happen on your project:
-
Are there signs of efflorescence now?
-
Is the property properly drained?
-
Does surface water run towards the foundation?
-
Is there a French drain system?
-
How old is the slab, what time of year was it poured?
-
Was the concrete placed on a saturated sub grade?
-
Was the concrete placed directly on a vapor retarder?
-
Was a granular material placed over the vapor retarder (vapor barrier being the outdated term) and was the base saturated?
-
If a vapor retarder was used, was it carefully taped at penetrations, around the plumbing, for instance? Did the mix design include fly ash?
-
Was a waterproofing admixture used?
-
Was calcium chloride used?
-
How much "water of convenience" was added to the concrete?
-
Was a curing compound or liquid densifier applied?
Answers to at least some of these questions can give a decorative contractor a heads up before wading into a project completely uninformed and unprepared.
More accurate, but also more expensive, testing technology such as the Protimeter Moisture Measurement System (ASTM Standard F-2170-02) uses a probe to measure the presence of moisture on and below the concrete surface along with the relative humidity, dew point and temperature. Two non invasive hand held devices using similar technology are the Aquant, which measures surface moisture to a depth of 10 – 20 mm and the Tramex Concrete Encounter Moisture Meter which transmits a signal ½" deep and projects a moisture measurement for 4". The benefit of these tools is their accuracy in measuring the moisture levels well beneath the surface whether there is any current movement or not. Given the financial risk, not to mention damage to a contractor's reputation it makes sense for a contractor to explore procedures that more clearly indicate subsurface conditions in order to avoid the efflorescence problems caused by moisture.
We mentioned that a well drained site and a vapor retarder are deterrents to efflorescence. The case can be made for placing the concrete directly on the vapor retarder or over granular material on top of the vapor retarder. The argument against the granular material is that it may become a saturated "blotter" before the slab is poured adding even more water that has only one way to leave. Finishers argue that there will be too much bleed water resulting in dusting, but a 4" slump with water reducers and a well graded mix will show very little bleed water. Elevated slabs are quite common in commercial construction and they are not placed on a blotter material. The really important factor here is minimizing water in all the important areas...the sub grade, the concrete and the procedures performed by the decorative contractor. These all require some amount of water, but keeping water to a minimum helps ensure that efflorescence is controllable.
To give an idea how much water may be available to bring soluble salts to the surface when these factors are not given any consideration let us consider a typical residential slab pour...assume we have a 2" thick blotter course of sand residing between the concrete slab and a vapor retarder. Dry sand weighs approximately 100 pounds per cubic foot. Wetted to achieve compaction, this sand could easily contain 10% moisture by weight, or 10 pounds of water per cubic foot of sand. It will take approximately 167 cubic feet of sand to cover 1,000 square feet of vapor retarder. That figures out to each 1,000 square feet of concrete surface having 1,670 pounds, or 200 gallons of water sitting on the underside of the slab with no where to go but up! Add that amount of water to another 60 or 70 extra gallons of "water of convenience" added by the finisher and we may have 270 gallons of extra water moving towards the surface whenever surface conditions are warmer or drier than the slab itself. There is another aspect of this foreboding picture...this porous slab we have described acts like a hard sponge with large pores and capillaries throughout the matrix, able to wick moisture up and quite willing to act as a hard sponge, capable of absorbing hundreds of pound of water from the cleaning processes employed by the decorative flooring contractor.
WHAT OPTIONS DOES A STAINER HAVE?
Technology that might offer double relief from efflorescence related issues involves the use of chemical liquid densifiers and hardeners. First, manufacturers say chemically hardened floors do not require a membrane sealer. This eliminates the trapped efflorescence problem and also greatly reduces maintenance costs. The chemicals include silicates, silicaonates, polysiliconates, silanes, siloxanes and the new lithiums, to name a few. Some of these are used in the conjunction with polished concrete floors. Some are used on floors already acid stained or dye stained and could receive a membrane type sealer. Some of these chemicals have been used for years and some are relatively new to market. Claims vary from product to product and from manufacturer about how far the chemicals penetrate, their permanence and the levels of shine and slip resistance. We know for certain that the big box stores are getting away from vinyl and going to bare concrete. Decorative floor contractors would be well served to explore this technology even for smaller residential stained floors.
Secondly, some contractors are following the application of acid stains with silicate type non-film forming sealers generically described as chemical hardeners, densifiers and soluble chloride reducers within a few days of concrete placement. Efflorescence is reduced as the silicate causes the matrix to become denser as we described earlier. The contractor has the option of adding conventional membrane forming sealers if subsequent VTR tests indicate acceptable levels.
Doug Bannister is owner of The Stamp Store in Oklahoma City, OK, which provides a complete line of decorative concrete materials including products, equipment and training. www.thestampstore.com
EFFLORESCENCE Q&As
Chris Sullivan is a decorative concrete expert who answers technical questions from contractors and homeowners concerning efflorescence and other issues.